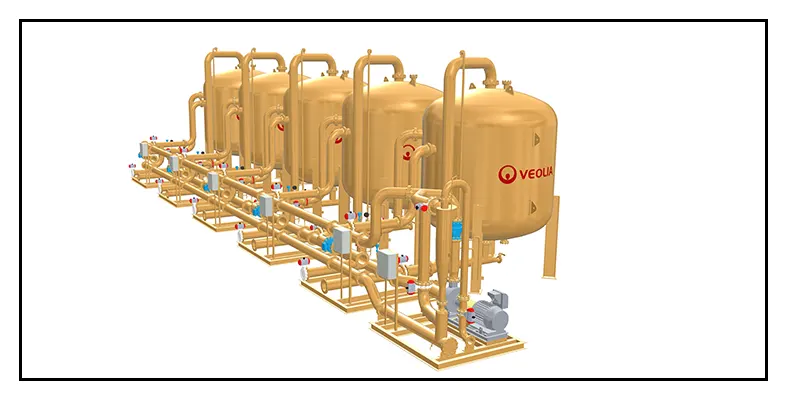
The filtration system provides 98% solids removal efficiency. (Image source: Veolia Water Technologies)
Veolia Water Technologies, a global leader in produced water treatment, has launched ToroJet, a nutshell filtration system treating produced water in the oil and gas industry for reinjection, reuse or discharge
The filtration system provides 98% solids removal efficiency and reduces hydrocarbon concentrations to less than 2 milligrams per litre. ToroJet introduces a media cleaning system at grade level, eliminating the need for top-mounted backwash equipment at each filter. This significantly reduces capital expenses and maximises asset utilisation, allowing plant operators to clean nutshell media with lower operational costs and minimal media losses. The system's design enhances safety by providing easy access for maintenance.
The ToroJet system offers modular components that facilitate staged project expansions, ensuring operators can adapt to future needs without significant disruptions. The shared cleaning skid enables efficient media cleaning across multiple vessels, minimising downtime and maximising productivity. A fluidisation pump complying with API or ASME-ANSI standards provides consistent media cleaning every cycle.
ToroJet eliminates bulky platforms and ladders, allowing for a lower profile design that reduces building size and costs while improving safety and ergonomics for operators and technicians.
“ToroJet is the result of our extensive research and development program aimed at optimising nutshell media filtration to meet the evolving demands of our clients,” said Oscar Velastegui, Veolia Water Technologies North America vice president in charge of Filtration Technology. “We are proud to offer a solution that improves the current technology and sets a new standard for produced water polishing. ToroJet revolutionises traditional nutshell filtration by offering a simpler, safer, and more cost-effective solution."