In The Spotlight

The initiative brings together a range of powerful, scalable, modular solutions designed for the Middle East’s manufacturing landscape. (Image source: Adobe Stock)
Omnix International, a leader in digital transformation and innovative technology solutions, is expanding its its Digitization in Manufacturing initiative to address the growing demand for intelligent, immersive, and future-ready production ecosystems and help manufacturers move into the era of Industry 5.0
Omnix’s Digitization in Manufacturing initiative brings together a range of powerful, scalable, modular solutions designed for the Middle East’s manufacturing landscape, that can be tailored for manufacturers across sectors such as oil and gas, automotive, aerospace, electronics, and other manufacturing. Offferings range from smart factory enablement to enable predictive and autonomous operations, to immersive technologies to boost collaboration and workforce efficiency, digital twin platforms for real-time monitoring, optimisation and predictive maintnance, and AI-powered insights for proactive decision making. The platform offers the ability to converge immersive design, engineering-grade simulations, advanced automation, and real-time operational visibility into a single, scalable framework, with a focus on helping customers integrate the most appropriate technologies for their needs.
The move comes at a time when increasing global challenges such as supply chains, rising energy and operational costs and skilled labour shortages are accelerating the move to agile, data-driven environments.
Walid Gomaa, CEO of Omnix said, “As a long-standing provider of solutions to the manufacturing industry, we see that many companies are under pressure to work towards incorporating faster, smarter and more sustainable solutions. Our goal is to help them reimagine production through intelligent digitisation where the focus is not only on automating processes but moving away from a fragmented production ecosystem to one which is integrated, predictive and human centric.”
Rizwan Kareem, business unit manager - Industry Support Solutions at Omnix, added, “We see value being provided by offering solutions that can help bridge our customers physical and digital needs and help them raise their decision making capabilities, increase operational efficiency and strengthen their work-force productivity. It is our way of seeing manufacturers pave their path towards Industry 5.0. Our strength lies in unifying design, automation, AI and XR into a single platform that helps customers achieve their strategic goals.”
Integrated pilot environments are underway at key customer sites that are incorporating the new capabilities, across the UAE, KSA, Qatar, Kuwait and Oman.
The company aims to work alongside regulators, academia and technology partners to foster a regional ecosystem, enabling upskilling through immersive learning and being in a strong position to deliver full lifecycle digital services from consulting and solution architecture to deployment of change management.

The range covers all applications from residential to industrial environments. (Image source: Adobe Stock)
Teledyne Gas & Flame Detection (Teledyne GFD) gas has launched its new MethaSense range of battery-powered methane detectors, comprising three models using cutting-edge NDIR (non-dispersive infrared) sensor technology for reliable and precise methane detection
MethaSense, designed for residential and commercial applications, is a compact, wireless natural gas detector with a range of 0-5 % volume, featuring accurate detection without false alarms, and immediate alerts through integrated audible and visual alarms. With progressive signal processing algorithms, MethaSense detects, alarms and monitors methane at concentrations as low as 10% of the lower explosive limit (LEL) for enhanced safety. Optional wireless (LoRaWAN) connectivity enables real-time gas detection visualisation, providing clear, actionable insights.
MethaSense XP is engineered for industrial environments where robust performance and reliability are essential. MethaSense XP’s rugged design and reliable detection capabilities ensure worker safety and operational continuity, especially in areas where maintenance access is limited.
It combines the same advanced NDIR sensor technology with enhanced durability and wireless communication options, including LoRaWAN, NB-IoT and Bluetooth. MethaSense XP again features audible and visual alarms, while its 10+ year battery autonomy and immunity to corrosion and saturation make the detector ideal for continuous safety monitoring in demanding conditions. With ATEX and IECEx certifications, MethaSense XP operates reliably in hazardous zones.
MethaSense Trace is a high-performance methane detector for LDAR (leak detection and repair) and utility applications, where accurate and autonomous methane monitoring is essential for regulatory compliance and environmental protection. A rugged build with IP67 ingress protection rating for outdoor use ensure uninterrupted performance in harsh conditions, reducing operational risks and maintenance costs.
With exceptional methane sensitivity, it provides 10× higher methane selectivity than previous-generation sensors, with a detection range that extends from 50 ppm to 100% volume for both low-emission environmental monitoring and high-concentration safety thresholds.
The detector delivers 24/7 methane emission monitoring, detection and quantification across large-scale industrial sites. By combining real-time sensing, cloud-based analytics and automated reporting, MethaSense Trace enables operators to detect, localise and measure methane emissions with precision. This not only helps reduce emissions but also ensures full compliance with new methane regulations.
“NDIR technology, as utilised by all three detectors in our new MethaSense series, offers high selectivity, fast response times and long-term reliability,” explained Régis Prevost, product line manager, Teledyne GFD. “Users benefit from natural gas detectors that provide a low-maintenance, cost-effective, versatile solution for continuous methane monitoring, supported by key features that include up to 10+ years of battery life, zero recalibration requirements, wireless connectivity options, and suitability for smart infrastructure and safety-critical environments.”
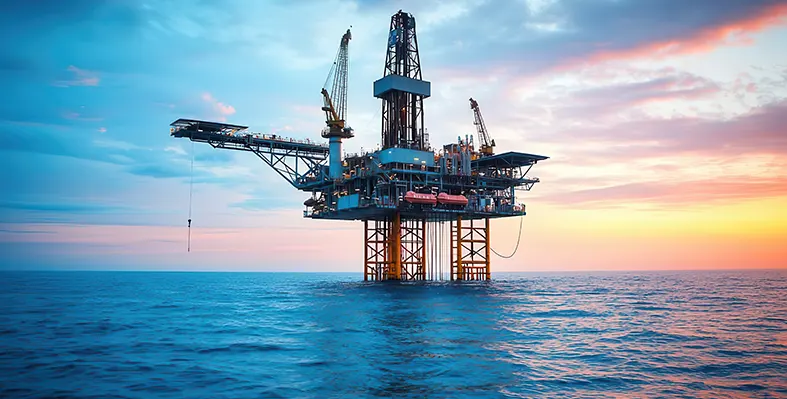
Oil and gas operations in the Middle East span harsh deserts, sprawling refineries and high-risk offshore environments. (Image source: Adobe Stock)
In the oil and gas industry, where every second counts and every decision impacts profitability and safety, robust security is not just a luxury – it's a necessity
From protecting critical assets to safeguarding human lives, security systems must meet the highest standards of reliability and performance.
Pelco, a leader in video security, is uniquely positioned to address the challenges faced by oil and gas companies in the Middle East, offering a fresh perspective on how to optimise security systems seamlessly. With our upcoming online event, we invite you to explore how Pelco can help tackle worker safety, asset protection and operational efficiency in this complex industry.
Addressing oil and gas challenges head-on
Oil and gas operations in the Middle East span harsh deserts, sprawling refineries and high-risk offshore environments. Physical, environmental and digital threats are converging, and security systems must evolve to meet these overlapping demands. Our upcoming online event will focus on three critical areas where Pelco's expertise can make a difference:
1. Improve worker safety and HSE compliance
Ensuring worker safety is both a moral responsibility and a regulatory imperative. Health, Safety and Environmental (HSE) compliance is a top priority for oil and gas operations. Pelco's advanced portfolio is designed to help you meet these standards.
Edge-based analytics and intelligent video security can be valuable tools in supporting site safety. These systems can help detect safety incidents, such as slips or falls, especially in areas where oily surfaces, heat or dust create additional hazards. When incidents occur in remote areas, automated detection can prompt faster intervention, thereby closing the gap between the event and the response.
Personal Protective Equipment (PPE) compliance is another key safety concern. High temperatures in the Middle East can lead to discomfort, and in some cases, workers may be tempted to remove protective gear, such as hard hats or vests, for temporary relief. In this case, AI-enabled video analytics can help identify instances of non-compliance, enabling safety teams to address the issue before it becomes a liability.
Zone-based behavioural analytics can help detect when someone enters a restricted or hazardous area or remains in a dangerous zone longer than necessary. For example, loitering detection near flare stacks or storage tanks can support situational awareness and proactive incident mitigation.
2. Improve security and asset protection
From refineries in the desert to offshore rigs in corrosive marine environments, your assets operate under pressure, so your security systems must withstand these harsh conditions. In areas where explosive gases or dust particles may be present, even basic equipment can pose risks. That’s why choosing video solutions built for hazardous environments is critical.
ExSite Enhanced cameras, featuring 316L stainless steel construction and certifications such as ATEX and IECEx, are designed for use in hazardous atmospheres. Whether it’s observing pipeline manifolds, wellheads or chemical storage areas, these systems deliver dependable performance in high-risk environments. In corrosive coastal locations, such as LNG terminals or offshore rigs, Pelco’s anti-corrosion models withstand salt spray, humidity and chemical exposure without compromising visibility.
For perimeter defence, long-range Silent Sentinel cameras give security teams early warning of approaching threats, detecting vehicles, vessels or drones from kilometres away in fog, darkness or dust. These systems are especially valuable for remote desert pipelines or unstaffed offshore installations, where rapid detection is critical to prevent disruptions.
3. Minimise downtime and maximise uptime
Every minute of downtime impacts revenue. For oil and gas operations, the cost of unplanned outages is measured in millions of dollars. With Pelco, your video security can become an operational asset.
Radiometric thermal cameras can detect overheating in transformers, compressors and electrical panels, allowing teams to take action before equipment failure occurs. At the same time, Pelco’s camera image health analytics help ensure your video infrastructure is always performing at its best. Our cameras automatically detect issues such as lens obstructions, misalignment or tampering, reducing the need for manual inspections and helping ensure your security coverage is always clear, optimised and ready when it matters most.
Join us to discover the Pelco advantage
We invite you to join our upcoming online event, where industry leaders and Pelco experts will dive deeper into these challenges and solutions. Together, we'll explore how Pelco can be the missing ingredient to supercharge your security and drive operational excellence in the Middle East oil and gas sector.
Don't miss this opportunity to gain actionable insights and position your operations for success. Register now and discover how Pelco can transform your approach to security.
-
GPT Industries - Iso-Smart
-
ADIPEC 2024 - Exclusive Interview with Joseph El Bitar, Hexagon
-
ADIPEC 2024 - Exclusive Interview with Alexander van Veldhoven, Bapco Energies
-
ADIPEC 2024 - Exclusive Interview with Friedrich Portner, Safeen Group
-
ADIPEC 2024 - Exclusive Interview with Kevin Brilz, Fishbones
-
ADIPEC 2024 - Exclusive Interview with Mohamed Malak, Fishbones
-
ADIPEC 2024 - Exclusive Interview with Dileep Divakaran, SLB
-
ADIPEC 2024 - Exclusive Interview with Eric Kjol, SLB
-
ADIPEC 2024 - Exclusive Interview with Dmitry Shubenok & Aleksandr Dolgikh, North Side
-
ADIPEC 2024 - Exclusive Interview with Adam Stephenson, AkzoNobel
-
ADIPEC 2024 - Exclusive Interview with Frazer Young, Oil States
-
ADIPEC 2024 - Exclusive Interview with Peter Foith, CS Combustion Solutions GmbH
-
Exclusive interview with Maurits van Tol
-
Rockwell Automation interview with Sebastien Grau
-
Rockwell Automation interview with Michael Sweet
-
ADIPEC 2023 - Exclusive interview with Wissam Chehabi, Fishbones
-
Rockwell Automation interview with Kalypso’s Rodrigo Alves & Knowledge Lens’ Ganesh Iyer
Dana Gas has reported success in the initial stages of its US$100mn investment programme to increase Egypt’s gas production
The US$100mn investment programme, which involves the drilling of 11 new wells, is expected to significantly increase Dana Gas’s long-term production in Egypt and add approximately 80 bcf in recoverable gas reserves over the course of the two-year plan.
The company has received encouraging initial results from the ‘Begonia-2’ appraisal well, the first appraisal well within the Begonia development area in Egypt’s onshore Nile delta and the first of eleven appraisal and exploration wells planned under the investment programme. The well is estimated to contain nine billion cubic feet (bcf) of gas as an initial estimate, which is subject to increase. Begonia-2 will produce an additional five million cubic feet per day. The well is located in the "New El-Manzala" concession and is operated by the El-Wastani Petroleum Company (Wasco).
The company has also begun to re-complete several wells in other geological layers, which are expected to add more reserves and enhance production. Work is currently underway on the Balsam-3 well, where estimated reserves are 4 bcf, with an anticipated additional production of 3 million cubic feet of gas per day. The successful recompletion of Balsam-3 is expected to reduce the risk associated with drilling exploration wells in the area and further enhance output.
Richard Hall, CEO, Dana Gas, said, “We have been developing and producing gas in Egypt for over a decade, and the signing of the concession area consolidation agreement with the Egyptian Natural Gas Holding Company (EGAS) late last year has allowed us to acquire additional areas under improved financial terms, enabling us to launch this new phase.
“The success of drilling this well opens vast prospects for gas production in the 'Begonia' area and presents promising future opportunities for expansion and growth. It will also extend the operational life of our assets in Egypt. We are fully committed to making every effort to ensure the success of the programme and its efficient and timely execution. Dana Gas reaffirms its strong commitment to reinvesting the payments it receives from the Egyptian government into executing this ambitious programme and supporting future development projects in the country.”
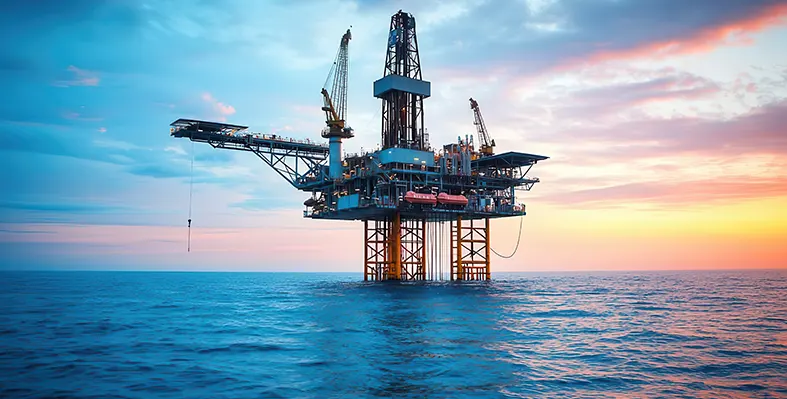
The Association has seen an uptake in its qualifications in sectors including oil and gas. (Image source: Adobe Stock)
The Association for Project Management (APM) has seen a 35% growth in membership numbers in the region in the six months since establishing its regional network in the UAE
Over this period, APM also successfully conducted several networking events and educational webinars, as well as launching a pilot of its popular Project Fundamentals Qualification in Arabic.
APM’s director of Education and Lifelong Learning, Jackie Martin, said, “We are witnessing an unprecedented demand for project management professionals in the region due to increase in infrastructure projects, economic diversification and business transformation initiatives, all of which require qualified managers. The sectors that have seen the most uptake for our qualifications include construction, oil and gas, energy, engineering, and infrastructure. With growth in sustainability practices and AI adoption, project managers need to upskill to face the demands of a rapidly changing workforce, and we have several programmes to guide them through this industry transformation.”
APM’s Project Management Qualification and Chartered Project Professional (ChPP) status have also seen a growing interest from the region. The Project Management Qualification, which is designed for individuals with some experience in project management, aims to enhance knowledge and skills in all areas of project management. It covers key areas like planning, risk management and communication, and is a valuable credential for career advancement for professionals in all industry sectors. ChPP status shows a person has achieved the highest standard of expertise and proven exceptional project capabilities, through a defined level of technical knowledge, professional practice and ethical behaviour.
Miriam Al-Alawi, deputy network lead for APM in the UAE, said, “APM membership gives one access to qualifications, networking and events to research, resources and debate – all aiding a project professional’s ongoing career development.”
APM UAE Regional Network member, Rachael Keeble, founder of BuiltWell, added, “By launching in the UAE, APM are playing an important role bringing together project management professionals for networking, debate and discussion. I was delighted to be part of the recent ‘Women in Leadership’ panel which explored the themes of inclusive leadership, various leadership styles and how we can best empower and advocate for others. The key takeaway was that authenticity, passion and empathy have an important place in leadership and the success of our projects."
Upcoming APM programmes in the region
To help project managers prepare to face the challenges of a rapidly transforming workforce, APM is offering a free-to-attend webinar on ‘Career development tools and techniques’ on 2 September, 2025. To register, please click here.
The APM Project Fundamentals Qualification is now being offered in Arabic, specifically for the UAE and Middle East region, with a pilot programme taking place in September 2025. Project professionals who use Arabic, and would like to gain the APM Fundamentals Qualification, can find out more information and apply to join the pilot here.
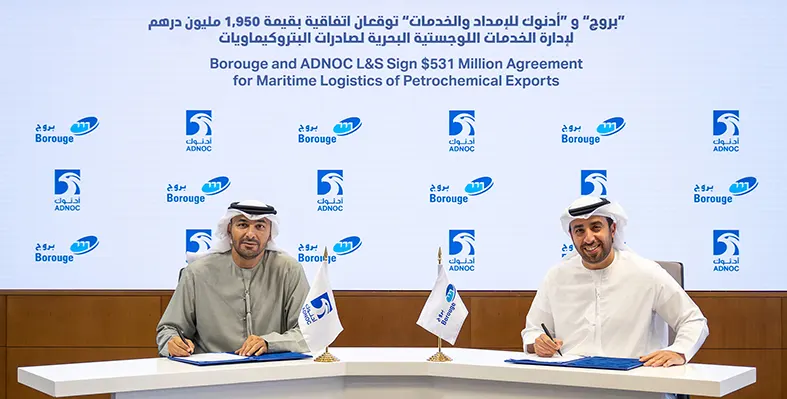
ADNOC L&S will manage the transportation of up to 70% of Borouge's annual production. (Image source: ADNOC L&S)
Borouge Plc and ADNOC Logistics & Services Plc have partnered to boost the production and export of petrochemicals from the UAE, as Borouge prepares to ramp up production capacity
Borouge plans to increase production capacity by 1.4 million tonnes per annum by the end of 2026 through its Borouge 4 mega project, which will make it the world’s largest single-site polyolefin complex. The 15-year US$531mn service agreement, which will drive cost savings and efficiencies as well as enhancing Borouge’s supply chain network, covers port management, container handling, and feeder container ship services for the Borouge Container Terminal in Al Ruwais Industrial City, Abu Dhabi. ADNOC L&S will manage the transportation of up to 70% of Borouge’s annual production, deploying a minimum of two dedicated container feeder ships to transport Borouge’s products from Al Ruwais to the deepwater ports of Jebel Ali in Dubai and Khalifa Port in Abu Dhabi.
Hazeem Sultan Al Suwaidi, CEO of Borouge, commented, “This agreement builds on our longstanding collaboration with ADNOC L&S, a partnership that has been instrumental in meeting the evolving needs of our customers in high-growth markets. It brings significant benefits to Borouge; driving substantial operational cost savings and enhancing our Logistics Variable Cost (LVC), as well as complementing our existing rail operations and expanding the flexibility of our supply chain network. With the rapid increase in our production capacity, we are advancing our capabilities in delivering differentiated products and solutions efficiently, while keeping pace with rising global demand."
Captain Abdulkareem Al Masabi, CEO of ADNOC L&S, added, “This comprehensive container terminal agreement marks a major milestone in our successful partnership with Borouge, delivering on ADNOC L&S’ strategy to provide seamless, end-to-end logistics solutions that power the UAE’s industrial growth and export ambitions. By leveraging our extensive maritime and logistics expertise, we are ensuring that Borouge’s world-class petrochemical products reach global markets efficiently and competitively.”
The global adoption of Industrial AI is accelerating rapidly, and is set to double from 32% to 59% within 12 months, according to a recent study from IFS, a leading provider of Industrial AI Sofware
However, according to The IFS Invisible Revolution Study 2025*, which surveyed over 1,700 senior decision makers at industrial enterprises globally, organisations are not fully prepared for its full implementation, creating what IFS calls the ‘AI Execution Gap,’ with 52% of senior leaders saying their management teams don’t fully understand AI, and 99% of global workforces requiring major reskilling to scale AI impact.
“AI is a core driver of business performance, it’s time to plug the AI Execution Gap – bring people, process and product together to deliver tangible outcomes,” said Kriti Sharma, CEO, IFS Nexus Black. “The pace of adoption is inspiring, but the next big unlock will come from scaling trust, strategy, and talent. Industrial AI is a powerful force for good, and we’re in a moment of opportunity: those who move fast will lead the next decade of industry.”
More than half of business leaders (53%) admit their organisation still lacks a clear AI strategy, yet the study clearly highlights the benefits available to companies that embrace AI. 70% of businesses report better-than-expected ROI from their AI investments, and on average 88% say AI has already improved profitability. Training and upskilling will be key to ensuring that industrial companies remain relevant.
Despite growing confidence in AI’s potential, there are still issues with trust. Only 29% of global leaders are comfortable allowing AI to make strategic decisions autonomously, while 68% say a human must still confirm or approve AI-generated outputs. Concerns about bias also persist. 65% of global leaders support the creation of an independent, international AI regulatory body to help close the trust gap.
Business model shift
The report highlights how Industrial AI is changing how businesses are run, automating maintenance, predicting disruptions, optimising supply chains, and facilitating intelligent decision-making across field service, asset management, and manufacturing. 54% of global organisations are using automation AI, while 45% are deploying predictive AI. Already, 35% are experimenting with Agentic AI, capable of autonomously executing decisions across workflows. Traditional business models are being influenced by AI with 77% of global leaders saying it is accelerating servitisation, the evolution from product sales to outcome-based services, where businesses deliver uptime, performance, and continuous value instead of just physical goods.
Sharma continued, “Industrial AI is moving into real-time, decision-grade intelligence embedded across the enterprise. It’s already securely automating the complex, predicting the unexpected, and powering new service-led business models. This is about shifting from tasks to transformation, and the organisations who embrace that shift will lead the next industrial chapter.”
Oil Review Middle East hosted a very well-attended webinar on 20 November on the future of offshore operations, in association with SAFEEN Group, part of AD Ports Group
The webinar explored the latest trends and challenges in the rapidly evolving world of offshore operations, focusing on groundbreaking innovations that are driving sustainable and efficient practices. In particular, it highlighted SAFEEN Green – a revolutionary unmanned surface vessel (USV), setting new benchmarks for sustainable and efficient maritime operations.
Erik Tonne, MD and head of Market Analysis at Clarksons, gave an overview of the offshore market, highlighting that current oil price levels are supportive for offshore developments, and global offshore capex is increasing strongly. The Middle East region will see significant capex increase over the coming years, with the need for rigs and vessels likely to remain high. Offshore wind is also seeing increased spending. Global rig activity is growing, while the subsea EPC backlog has never been higher, with regional EPC contracts seeing very high activity. Tonne forecast that demand for subsea vessels and other support vessels will continue to increase.
Tareq Abdulla Al Marzooqi, CEO SAFEEN Subsea, AD Ports Group, introduced SAFEEN Subsea, a joint venture with NMDC, which offers reliable and innovative survey, subsea and offshore solutions to support major offshore and EPC projects across the region. He highlighted the company’s commitment to sustainability, internationalisation and local content, and how it is a hub for innovations and new ideas, taking conceptual designs and converting them to commercial projects. A key project is SAFEEN Green, which offers an optimised inspection and survey solution.
Tareq Al Marzooqi and Ronald J Kraft, CTO, Sovereign Global Solutions ME and RC Dock Engineering BV. outlined the benefits and capabilities of SAFEEN Green as compared with commercial vessels, in terms of safety, efficiency, profitability and sustainability. It is 30-40% more efficient through the use of advanced technologies, provides a safer working environment given it is operated 24/7 remotely from a control centre, and offers swappable payload capacity. Vessels are containerised and can be transported easily to other regions. In terms of fuel consumption, the vessel is environment-friendly and highly competitive, reducing emissions by 90% compared with conventional vessels, with the ability to operate on 100% biofuel.
As for future plans, SAFEEN Green 2.0 is under development, which will be capable of carrying two inspection work-class ROVs simultaneously. A priority will be to collect data to create functional AI models for vessels and operations, with the first agent-controlled payload systems in prospect by around 2027.
To view the webinar, go to https://alaincharles.zoom.us/rec/share/mNHjZhAhQzn1sPzmFWZCgrq7_SckfLRcSb4w81I7aVlokO9sgHM_zVeOqgN3DgJS.bO4OIRqNeFP09SPu?startTime=1732095689000
Oil and gas companies are playing a leading role in the development of carbon capture, utilisation, and storage (CCUS) according to a new report from GlobalData
CCUS is widely gaining credence as an important energy transition strategy, given its potential to decarbonise hard-to-abate sectors such as cement, steel, refining, and thermal power generation.
As of 2024, more than 70% of the operational and planned CCUS facilities were associated with energy assets, according to the GlobalData’s Strategic Intelligence report, “Carbon Capture and Storage", indicating a growing commitment by the energy sector to reduce its emissions intensity through innovation in carbon capture and storage technologies. The global energy sector accounted for more than 50 commercial-scale carbon capture projects as of 2024, representing a cumulative carbon capture capacity of approximately 45 million tonnes per annum (MTPA). If all the proposed projects come to fruition, the global carbon capture capacity in the energy sector could rise to nearly 316 MTPA by 2030.
Leading oil and gas players such as ExxonMobil, Occidental Petroleum, and Equinor have taken early initiatives in CCUS, supported by engineering and service companies like Technip Energies, Mitsubishi Heavy Industries (MHI), and SLB. These firms are leveraging their expertise in industrial-scale project delivery to develop and execute carbon capture strategies across upstream and downstream operations. For example, Shell Catalysts & Technologies has signed an agreement with Technip Energies to deliver a post-combustion amine-based carbon catpure solution using Shell's CANSOLV CO2 capture system, designed to make carbon capture more investable, scalable and accessible for industrial sectors and helping hard-to-abate industries to decarbonise.
According to GlobalData’s report, there are 17 carbon capture projects in advanced stages of development that are expected to begin operations later this year. Additionally, around 460 capture projects are under development globally across diverse industries, which will lead to significant capacity growth through 2030.
Middle East CCUS leadership
The Middle East is emerging as a major region for CCUS development. The UAE’s ADNOC operates Al Reyadah, the world’s first commercial scale operation to capture and store CO2 from the steel industry, with a capacity of 800,000 tonnes a year. Further projects are planned and underway such as Habshan, which will have a capture and storage capacity of 1.5MTPA and is set for completion in 2026. CO2 will be injected and placed for permanent storage in ADNOC Onshore’s Bab Far North Field, southwest of Abu Dhabi. ADNOC aims to capture and store 10MTPA of CO2 by 2030. Meanwhile while Aramco has a target of 14 MTPA by 2035, and is developing a major 9MTPA carbon capture hub at Jubail with SLB and Linde, set to be one of the largest in the world.
Ravindra Puranik, Oil and Gas analyst at GlobalData, commented, “Unlike consumer-driven clean energy trends, CCUS adoption is largely influenced by regulatory and economic frameworks, with limited visibility to end users. Policies such as the EU Emissions Trading System (ETS), Canada’s carbon pricing mechanism, and the US 45Q tax credit have been instrumental in unlocking commercial opportunities for CCUS. These frameworks have helped offset the high capital and operational costs of CCUS deployment, particularly in energy-intensive industries, and are driving the emergence of large-scale projects globally.”
Puranik noted however that CCUS still faces a range of challenges that threaten to hamper its scale-up, such as high upfront costs, the lack of fully developed CO₂ transport and storage infrastructure, and limited commercial applications for captured CO₂. Retrofitting existing facilities often adds further complexity, making project economics difficult without consistent policy support.
“Additionally, regulatory uncertainty around permitting processes, cross-border CO₂ transport, and long-term liability for stored carbon continues to pose risks for investors. Public scepticism also persists, with some critics viewing CCUS as a strategy to extend the life of fossil fuels rather than as a legitimate tool for emissions reduction. The absence of standardisation and the fragmented nature of the CCUS value chain further limit the ability to implement integrated, scalable solutions.”