CS Combustion Solutions recently enhanced the capacity and efficiency of a sulfuric acid production plant located in Africa’s Copperbelt region, where demand for sulfuric acid is crucial in mining applications such as leaching copper and cobalt
Faced with growing demand, the plant needed to increase production while reducing operational costs and improving reliability. Through targeted improvements, CS increased daily production from 2,200 to 3,000 tons and optimised the plant’s overall performance.
Challenges before optimisation
Prior to the upgrade, the plant faced several challenges, including incomplete combustion, which led to sulfur droplets fouling downstream equipment like the waste heat boiler (WHB) and catalyst beds, increasing system pressure and requiring frequent shutdowns for maintenance. Clogging issues with conventional pressure atomisers resulted in frequent, costly nozzle replacements, while poor droplet atomisation caused hotspots in the refractory lining, increasing wear and reducing reliability.
Key measures implemented
CS Combustion Solutions tackled these issues with the following measures:
1. Ultrasonic atomisation: Replacing pressure atomisers with ultrasonic nozzles reduced droplet size from 400 to 110 µm, which minimised fouling, improved combustion, and protected the refractory lining from localised heat.
2. Swirl bodies: Introducing swirl bodies created rotational motion in the combustion air, enhancing flame formation and leading to more efficient sulfur combustion.
3. VectorWall installation: Replacing the plant’s original baffle walls with a VectorWall improved mixing within the combustion chamber, reduced hotspots, and prevented unreacted sulfur carryover to downstream components.
4. CFD analysis: A Computational Fluid Dynamics (CFD) study simulated and optimized the modifications prior to implementation, ensuring targeted performance improvements.Results and benefits
With these enhancements, the plant boosted production capacity by 30%, enabling 40 tons of sulfur incineration per hour. The new configuration allows maintenance of sulfur guns without stopping operations, reducing downtime and saving US$160,000 annually by decreasing pressure drop. Additionally, precise ultrasonic atomisation prevented sulfur buildup on the refractory, extending its lifespan.
This case study highlights the importance of innovative combustion technologies and detailed pre-implementation analysis, offering valuable insights for facilities facing similar challenges in optimising sulfuric acid production.
Boosting efficiency in sulfuric acid production
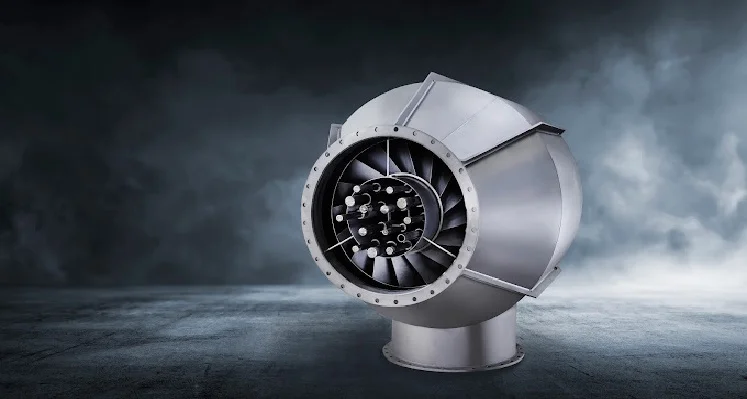
As a result of the upgrade, production increased and performance was optimised. (Image source: CS Combustion)