To meet today’s demands, utilities and industrial operators must transition to next-generation distribution systems, says Wael Gad, CEO and board member of Bawan Engineering Group
Frequent power outages, unexpected equipment failures, and rising maintenance costs are not just technical hiccups; they are business risks. As the CEO of a company that works extensively with various industries, I have seen these disruptions causing ripples across operations, delaying timelines, inflating budgets, and resulting in financial losses for my customers.
The pace at which energy demand is growing, combined with the increasing unpredictability of energy consumption, makes it clear that legacy systems are holding us back. It is time we treat power distribution as a strategic investment, not just an operational necessity.
Background
With the rise in manufacturing and the increasing use of machines, we have witnessed unprecedented transformations in various industries. As demand for industrial products has increased, factories have not kept pace in transforming their operations and equipment. As a result, industries have become inefficient and prone to breakdowns or failures.
A range of technologies and equipment ensures consistent operational readiness in critical industries, such as oil and gas (O&G), data centres, and other essential manufacturing applications. As a T&D expert, my focus is on power distribution infrastructure and its crucial role in ensuring the reliability of your manufacturing site. At the distribution level, switchgear is one of the most critical components, guaranteeing the safety of the entire network. However, ageing switchgear systems, limited automation, and reactive maintenance strategies have led to operational inefficiencies and frequent service disruptions in industries.
These issues result in prolonged power outages, decreased system reliability, and increased operational and maintenance (O&M) costs. Furthermore, outdated or insufficient electrical switchgear is a primary contributor to these inefficiencies, as it is essential for fault isolation, protection, and control functions. As a result, grid stability is compromised, leading to lower customer satisfaction and reduced system performance.
Why traditional switchgear no longer meets the needs of modern power systems
Now that we have outlined the problem and its impact, it is important to take a step back and ask: why is this happening in the first place? The answer lies in the limitations of traditional low-voltage (LV) and medium-voltage (MV) switchgear. Let’s take a closer look at some of the most critical shortcomings.
Lack of real-time visibility
Traditional switchgear gives you a binary view: on or off, fault or no fault. In dynamic industrial and manufacturing operations, these indicators are insufficient to assess the health of distribution assets.
Unpredictable maintenance and costly downtime
In my experience, unplanned outages can disrupt an entire production cycle or compromise service-level agreements (SLAs), resulting in high costs.
Slow response times and manual operations
In the event of faults or load imbalances, traditional systems primarily rely on field inspections to identify and address issues. The field team is dispatched without a definite fault location, delays recovery, and exposes personnel to hazards. Even a minute lost in response time can lead to increased disturbances in the system and negatively impact customer relationships.
Difficulties integrating modern energy systems
As electrical grids move toward decentralisation, integrating distributed energy resources, such as solar, wind, and battery storage, into the grid has become an imperative general practice. With the increasing number of installations having unknown risks, the traditional switchgear may not be able to handle this level of complexity.
Traditional switchgear solutions lack the ability to consistently communicate. Therefore, it becomes difficult for effective energy management systems and smart grid smarty pants to be very effective.
Turning challenges into opportunities
To meet today’s demands, whether it’s reducing downtime, improving safety, supporting the integration of renewable energy, or enabling advanced grid automation, utilities and industrial operators must transition to next-generation low- and medium-voltage switchgear. Smart switchgear turns traditional pain points into performance gains. Here’s how:
Maximised system reliability and lesser downtime
Smart switchgear solutions significantly enhance system uptime by identifying and mitigating faults before they impact operations. Predictive analytics and continuous monitoring enable preemptive maintenance, thereby reducing the need for emergency responses and minimising business disruptions.
With real-time fault location and the ability to switch remotely, engineers can achieve faster resolution times. In any industrial setting, where time is money, UTEC's solutions offer productivity and service availability by automating recovery while minimising manhours.
Extended lifespan of equipment
From a capital allocation perspective, extending the lifespan of electrical infrastructure is a game-changer. Intelligent switchgear continuously self-monitors, tracking insulation quality, temperature, and load conditions.
The result? We can replace or maintain components before they fail. Adopting a condition-based maintenance approach has effectively moved from reactive to proactive asset management. In financial terms, that translates to decades of additional service life, lower replacement costs, and a better return on infrastructure investment.
Lower operational and maintenance costs (OPEX)
UTEC's switchgear technology substantially lowers operational expenditure as it features intelligent asset management. Remote diagnostics and real-time operational status have diminished the requirement for manual site visits and emergency maintenance.
UTEC switchgear features predictive analytics that reduce energy losses, thereby optimising resource utilisation and facilitating efficient power system operation, ultimately lowering OPEX
Improved energy efficiency
Maintaining optimal energy use with UTEC's switchgear means intelligent load balancing and monitoring energy flow residuals across the network. This saves technical losses, contributing to improved power factors that support sustainability goals and save money.
Combining UTEC's switchgear capabilities with EMS and SCADA ensures that power is always distributed effectively and adaptively during periods of peak demand or when loads change.
Intelligent distribution: a strategic advantage
We have seen how smart switchgear can transform outdated infrastructure into a strategic asset, resulting in enhanced performance, improved safety, and more informed decision-making.
In today’s fast-paced world, your infrastructure strategy is your business strategy. Upgrading to intelligent distribution solutions is not just about keeping the lights on; it is about unlocking efficiency, resilience, and growth.Wael Gad is the CEO and board member of Bawan Engineering Group, a subsidiary of Bawan Holding, a public listed KSA company. Bawan Engineering Group consists of several companies operating in the manufacturing and services of Electrical & Digitisation equipment (Transformers, Substations, Switchgears, e-Houses, Battery Energy Storage Systems (BESS) and Data Centres). Bawan Engineering Group sells its products in more than 20 countries across the world under the brand UTEC.
Wael has more than 30 years of diversified experience across Europe, Middle East and Africa leading several multinationals and regional organisations. He serves as a board member of several companies in Saudi and Egypt and has also served as an advisory board director and as a business development and governance advisor with several organisations. Previously Wael was the CEO of Philips Lighting in Saudi, the general manager of Microsoft MMD in Saudi & Yemen and also held several C-level assignments for Electrolux across EMEA.
Transforming reliability and efficiency with smart switchgear solutions
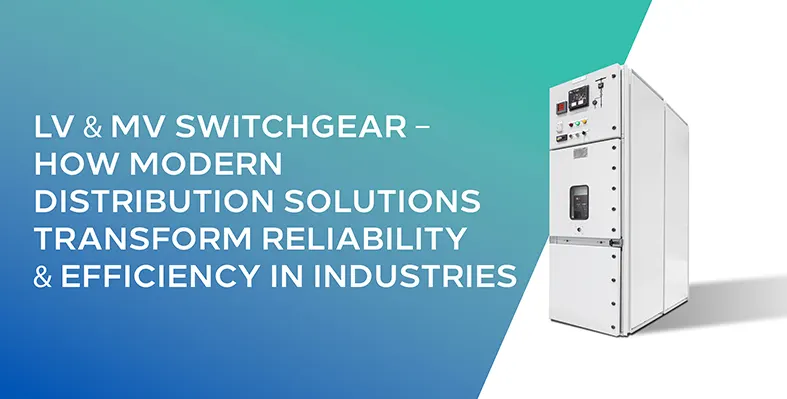
Utilities and industrial operators need to transition to next-generation distribution systems. (Image source: Bawan Engineering Group)