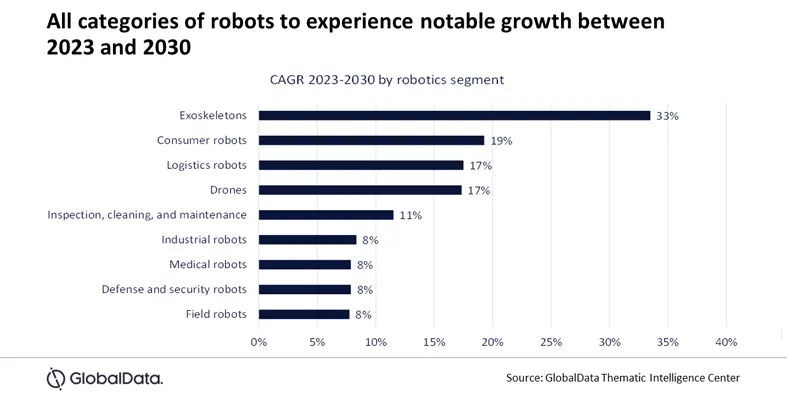
The oil and gas industry has emerged as a significant adopter of the technology. (Image source: GlobalData)
Data and analytics company GlobalData has released a thematic report, Robotics in Oil and Gas, which highlights the role of major oil and gas companies, such as ADNOC, BP, Eni, Equinor, ExxonMobil, Repsol, Rosneft, Shell, and TotalEnergies in the development and adoption of robotics to enhance safety and productivity on the field
With the applications of robotics continuously evolving, the oil and gas industry has emerged as a significant adopter of the technology to improve safety and efficiency of operations. According to the GlobalData report, robots equipped with advanced technologies are yielding increasingly positive results, bringing a continued transformation in the operations of oil and gas companies.
Ravindra Puranik, oil and gas analyst at GlobalData, said, “Robots are proving invaluable to execute complex tasks at production facilities, thereby protecting workers from hazardous environments and reducing the likelihood of costly shutdowns. As a result, companies such as Equinor, TotalEnergies, and Shell are deploying them to work alongside humans on offshore sites. For instance, robotic automation can manage remote operations, such as those conducted on Equinor's Oseberg H platform in the North Sea. Their ability to perform repetitive and mundane tasks with minimal errors is saving time and internal resources for companies. Furthermore, it allows them to deploy field technicians on more critical issues.”
Oil and gas operations are labor-intensive and involve numerous repetitive tasks, many of which occur in hazardous environments and face various obstacles. Robotics presents an excellent solution to many challenges within the industry, as they can handle more strenuous tasks and complex procedures more effectively than humans.
Puranik said, “Robots provide greater reliability and efficiency in completing assigned tasks while also enhancing operational safety. The integration of terrestrial, aerial, and underwater robots is already playing a crucial role in several high-stakes oil and gas projects throughout the value chain. French oil major TotalEnergies, in collaboration with Oceaneering, recently conducted a pilot inspection of subsea pipelines in the North Sea using autonomous underwater vehicles (AUVs).”
Robots can access hard-to-reach areas, carry out tasks beyond human capabilities, and operate continuously without needing breaks. Hence, they are being utilized as effective solutions for conducting inspections in difficult or hazardous environments, thereby avoiding preventing human exposure to such sites. Recently, cleaning of storage tanks is emerging as another prominent use case for robotics with companies, such as Saudi Aramco, Woodside, SK Innovation, and Indian Oil Corp, exploring the potential of robotic crawlers in this application.“Advancements in technology have equipped robots to effectively replace field personnel on oil rigs. Additionally, there is an increase in collaboration between oil and gas companies and technology vendors, enabling the diversification of robotic use cases with the integration of AI, IoT, cloud, and edge computing. These developments are anticipated to drive future growth in robotics within the oil and gas sector, reducing risks to human workers who operate alongside heavy machinery in often remote and challenging environments,” said Puranik.