In The Spotlight
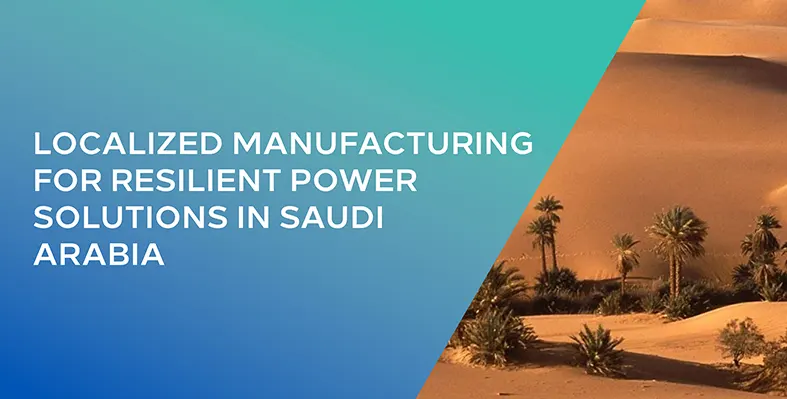
UTEC's products are specifically designed to integrate seamlessly with the regional grid. (Image source: UTEC)
Localised manufacturing for resilient power solutions in Saudi Arabia
Reliability begins with proximity. At UTEC, we are not just closer to our clients, but we are closer to the future Saudi Arabia is building.
Introduction
Saudi Arabia’s power transformation is no longer a vision; it’s happening fast. As the Kingdom advances toward a diversified and tech-driven economy, localised manufacturing is emerging as a vital enabler. At UTEC, we see it as a strategic imperative rather than just considering it a regulatory requirement. This approach enables national resilience, increased reliance on indigenous manufacturing capabilities, and supports accelerated infrastructure growth.
Today, I want to touch upon the current landscape of localisation in Saudi Arabia and its impact on the Transmission and Distribution (T&D) sector. Being a Saudi company, I would also be highlighting UTEC's role and contributions to the Kingdom’s ongoing economic transformation.
Why local manufacturing is a strategic advantage
The recent chaos, including supply chain backlogs and transport delays, has made our industry realise our excessive dependence on imported technologies. Localisation is fundamentally about regaining control. It reduces our dependence on overseas producers, shields us from global disruptions, and keeps our infrastructure plans on track.
As the CEO of a T&D equipment company, I have witnessed the impact of global supply chain disruptions on critical infrastructure timelines. The recent crises in Western markets have made us aware of the risks of over-reliance on equipment built and manufactured overseas. The events emphasised the point that the development of local capabilities is not only strategically beneficial but also a necessity.
Manufacturing power system technologies in the Kingdom, particularly critical equipment such as transformers and switchgear, are highly valuable. It enables us to complete projects more quickly, serve local stakeholders more effectively, and easily tailor our equipment to meet Saudi Arabia's grid and environmental requirements.
In my view, building an industrial base within the Kingdom is essential. Positioning economic value within our own borders not only strengthens our economy but also holds onto critical knowledge and drives innovation. With domestic demand growing, having robust capacity for production puts UTEC and Saudi Arabia more broadly well placed to enter international markets.
UTEC's commitment to local manufacturing and national growth
As Saudi Arabia advances its localisation agenda and strengthens its power infrastructure, UTEC stands as a long-term contributor to this vision. Our locally rooted operations, product expertise, and close alignment with national goals uniquely position us to support the Kingdom’s transformation in the transmission and distribution sector.
Saudi made
Over the last two decades, UTEC has been producing distribution transformers, unit substations, and medium-voltage switchgear in the Kingdom. Our operations are 100% Saudi-based, and our products are specifically designed to integrate seamlessly with the regional grid.
Engineering for local needs
Transformers and switchgear are not standardised products; they must be tailored to the working conditions of every project, the national standards for every targeted market, through local engineering expertise supported with global expertise and close liaison with clients, UTEC ensures that every system we supply is aligned with site conditions, regulatory compliance, and long-term performance expectations.
Reliable local support
Our domestic manufacturing model is also enhanced by after-sales service and lifecycle support, both of which are essential to ensuring long-term reliability. Customers know they can count on our professionals and technical experts to fix issues quickly and effectively when they inevitably arise. This level of responsiveness isn't typically available with overseas suppliers or off-the-shelf components.
Supporting the Kingdom’s vision
Our alignment with national objectives supporting the localisation efforts of the Ministry of Energy and the SEC's grid modernisation initiative ensures that solutions provided by UTEC meet evolving technical and operational standards, thereby future-proofing the Kingdom's infrastructure.
Empowering scalable power for national development
As Saudi Arabia launches some of the world's most ambitious industrial and infrastructure growth projects, including giga-cities and renewable energy initiatives, power systems must expand more rapidly than ever before.
With UTEC, we are working to turn this development into a reality. By manufacturing essential power equipment domestically, such as transformer bushings, as well as establishing the first factory in Saudi Arabia, we aim to alleviate project bottlenecks, minimise procurement risks, and accelerate project schedules.
We facilitate innovative projects, such as NEOM and the Red Sea Project, as well as industrial clusters, with expedited and superior-quality solutions that meet rigorous design, safety, and performance requirements.
In addition, with the Kingdom's increasing diversification of its energy mix through the addition of solar, wind, and hydrogen, the design of equipment needs to be more responsive and flexible. With a presence in the region, we are attuned to such evolution, enabling us to co-create with our partners and seamlessly adapt to changing systems and technical requirements.
Building human capital and technology capability
I believe localisation is not only the local manufacturing of goods, but also the enabling of local talent to create, innovate, and drive the future. It is for this reason that, at UTEC, we have ensured the engagement of local engineers, technicians, and managers in every aspect of our operations. Manpower localisation has also added value in cooperation with Saudi universities for internship programmes, followed by hiring.
It is critical to invest in daily training programmes, experiential technical courses, and continuous knowledge sharing. For me, factories are not simply manufacturing plants but also learning establishments that drive the kingdom’s industrial growth and sustained wealth.
Aligned with national vision—and going beyond
Saudi Arabia’s push for local manufacturing is not just a policy, but a clear national priority included in Vision 2030 and supported by frameworks such as the Local Content and Government Procurement Authority. At UTEC, we are proud to be at the forefront of this effort, not only achieving localisation targets but also exceeding them.
With every transformer and switchgear that we produce locally, we are enhancing the Kingdom's strategic direction. UTEC is creating economic value and helping the country move closer to energy independence. Our commitment goes beyond meeting local content mandates; we strive for excellence in local manufacturing within the power sector.
Beyond the Saudi market, our products are currently serving industries and utilities in more than 23 countries including the UK, Qatar, South America, and Kuwait. Transformers manufactured locally by UTEC are sought across diverse markets of the Middle East, Africa, and Europe. We are also making footprints in Asian economies. Our strong global presence is proof that Saudi Made is not just marked but has become a symbol of quality and innovation.
Conclusion: The future is local and built to last
Saudi Arabia is on an ambitious path towards a cleaner, brighter, and more sustainable energy future. Bringing the vision to life needs more than importing foreign solutions; it demands local commitment, capacity, and capability.
We at UTEC are proud to be a long-standing partner in the Kingdom's vision for energy. We pledge to provide high-quality and dependable power solutions, including transformers, switchgear, and associated electrical equipment, all of which are locally manufactured in Saudi Arabia. Our vision is not limited to serving the local market; we aim to contribute to making the Kingdom a regional hub for energy production and export.
With our partners, we are not just manufacturing equipment, but also fostering trust, and resilience, and laying the foundation for long-term self-sufficiency.
About Author:
Wael Gad, CEO, UTEC
Wael Gad is the CEO and Board Member of Bawan Engineering Group, a subsidiary of Bawan Holding, a public listed KSA company. Bawan Engineering Group consists of several companies operating in the manufacturing and services of Electrical & Digitization equipment (Transformers, Substations, Switchgears, e-Houses, Battery Energy Storage Systems (BESS) and Data Centers). Bawan Engineering Group sells its products in more than 20 countries across the world under the brand UTEC. Wael has more than 30 years of diversified experience across Europe, the Middle East and Africa, leading several multinationals and regional organizations. Wael serves as a board Member of several companies in Saudi & Egypt, he also served as an advisory board director and as a Business Development and governance Advisor with several organizations. Previously Wael was the CEO of Philips Lighting in Saudi, the General Manager of Microsoft MMD in Saudi & Yemen and he also held several C-level assignments for Electrolux across EMEA.
CCS at a turning point: DNV
Carbon capture and storage capacity is forecast to quadruple by 2030, and the Middle East has ‘significant CCS ambition’, according to a new report from DNV
Cumulative investment in carbon capture and storage (CCS) is expected to reach US$80bn over the next five years, according to DNV’s Energy Transition Outlook: CCS to 2050 report.
Up to now, growth has been limited and largely associated with pilot projects, but a sharp increase in capacity in the project pipeline indicates that CCS is at a turning point. CCS will grow from 41 MtCO2/yr captured and stored today to 1,300 MtCO2/yr in 2050, which will be 6% of global emissions, DNV forecasts.
The immediate rise in capacity is being driven by short-term scale up in North America and Europe, with natural gas processing still the main application for the technology. Europe is moving projects forward amidst tightening emissions regulations and developers are advancing in the US, taking advantage of the established 45Q tax credit. Hard to abate industries such as steel and cement production are forecast to be the main driver of growth from 2030 onwards, accounting for 41% of annual CO2 captured by mid-century. Maritime onboard capture is expected to scale from the 2040s in parts of the global shipping fleet.
As the technologies mature and scale, the average costs will drop by an average of 40% by 2050.
Ditlev Engel, CEO, Energy Systems at DNV said “Carbon capture and storage technologies are a necessity for ensuring that CO2 emitted by fossil-fuel combustion is stopped from reaching the atmosphere and for keeping the goals of the Paris Agreement alive. DNV’s first Energy Transition Outlook: CCS to 2050 report clearly shows that we are at a turning point in the development of this crucial technology.
“The biggest barrier to the very much needed acceleration of CCS deployment is policy uncertainty. Policy shifts, not technology or costs, have been responsible for many CCS project failures. However, policy support for CCS is firming across most world regions.”
Recent turmoil and budgetary pressure in the global economy pose risks to CCS deployment, potentially shifting priorities and removing necessary finance needed.
Jamie Burrows, Global Segment Lead CCUS, Energy Systems at DNV said “CCS is entering a pivotal decade and the scale of ambition and investment must increase dramatically. It remains essential for hard-to-decarbonise sectors like cement, steel, chemicals, and maritime transport. But as DNV’s report shows, delays in reducing carbon dioxide emissions will place an even greater burden on carbon dioxide removal technologies. To stay within climate targets, we must accelerate the deployment of all carbon management solutions -from industrial capture to nature-based removal - starting today."
Middle East developments
DNV notes that the Middle East is home to three operational CCS projects and six under construction. Operating facilities include the Al Reyadah steel plant in the UAE, Qatar's Ras Laffan LNG Facility, and Saudi Arabia's Uthmaniyah gas processing plant.
The world’s largest CO2 utilisation facility, United Jubail Petrochemical, is also in Saudi Arabia. The facility converts 0.5 MtCO2/yr into feedstock for chemical processes.
The main focus of regional CCS development has evolved from EOR to decarbonising energy and the production of low-carbon fuels. The UAE's Long Term Strategy highlights CCS as crucial for industrial sector decarbonisation, targeting 43.5 MtCO2/yr capacity by 2050. ADNOC aims for 10 MtCO2/yr captured by 2030 and net-zero operations by 2045. ADNOC's Habshan and Ghasha Concession projects, each with capacity of 1.5 MtCO2/yr, are currently under construction.
Saudi Arabia aims to capture and store 44 MtCO2/ yr by 2035 and launched a domestic carbon crediting scheme in 2024. A CCS hub is under construction at Jubail, which will store 9 MtCO2/yr by 2027 from natural gas processing and industrial sources in an onshore saline aquifer.
Oman aims to utilise its pipeline infrastructure for hydrogen and CO2 transport in new CCS and EOR projects.
Direct air capture (DAC) projects are emerging in Saudi Arabia, the UAE, and Oman, often combined with CO2 mineralisation or sustainable aviation fuel production.
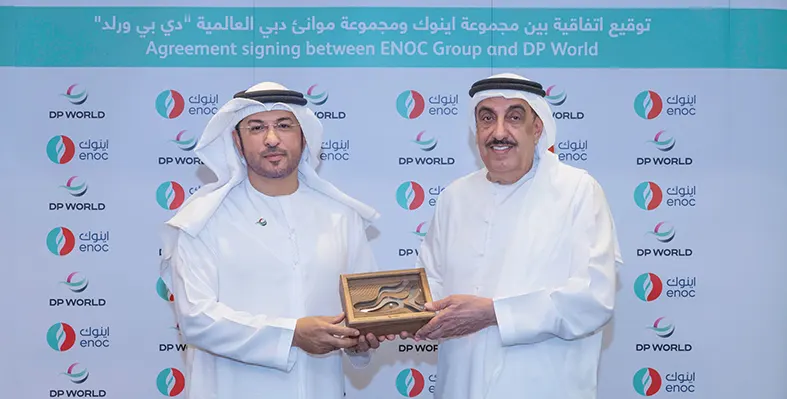
The agreement was signed by His Excellency Saif Humaid Al Falasi, Group CEO, ENOC, and His Excellency Abdulla Bin Damithan, CEO & managing Director, DP World GCC. (Image source: ENOC)
ENOC Group and DP World partner for emergency response
ENOC Group and DP World have signed an agreement to enhance emergency and fire response capabilities across Dubai’s energy and logistics infrastructure, through joint training, planning and coordination
The co-operation involves an annual joint exercise to enhance training, preparedness, and response times, led by ENOC and DP World's emergency teams. It also entails regular updates to emergency response plans and a shared protocol for engaging external parties to ensure swift and coordinated action.
ENOC Group continues to demonstrate its commitment to the highest levels of safety and emergency preparedness. In 2022, the Group launched an Emergency Response Centre in Jebel Ali in partnership with Dubai Civil Defence. More recently, members of ENOC’s Emergency Response Centre completed specialised training at the International Fire Training Centre in the UK, enhancing the Group’s HAZMAT and fire risk assessment capabilities. This advanced training equips firefighters with the skills to respond effectively to hazardous material incidents, perform complex rescue operations, and conduct fire risk assessments within the high-risk oil and gas sector. The group has specialised centres of excellence for delivering emergency response and crisis management and fire training services to corporate, segments and business units.
His Excellency Saif Humaid Al Falasi, Group CEO, ENOC, said, “This MoU marks a significant stride forward in solidifying our commitment to the highest safety standards and emergency preparedness. We are proud to collaborate with DP World, a partner who shares our deeply held values of ensuring operational safety and resilience across the board. This collaborative approach will undoubtedly enhance our collective ability to respond effectively to any unforeseen incidents, safeguarding our people, assets, and the community.”
His Excellency Abdulla Bin Damithan, CEO & managing director, DP World GCC said, “Safety is the core value that underpins everything we do at DP World. This agreement reflects our shared commitment to creating a safe environment for our people, assets and operations. Together with ENOC, we’re enhancing our ability to respond to emergencies and building more resilient, safe infrastructure to support regional trade.”