In The Spotlight
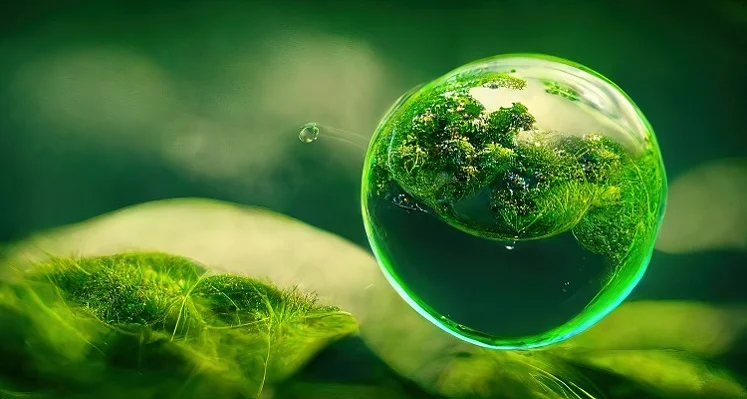
The UAE has launched its first initiative to inject CO₂ into deep saline aquifers for permanent geological sequestration.
Sven Kristian Hartvig, chief technology officer, RESMAN Energy Technology explains how the company’s advanced tracer technology is being used for CCS monitoring in Abu Dhabi’s saline aquifers
The UAE has launched its first initiative to inject CO₂ into deep saline aquifers for permanent geological sequestration. This inaugural industrial-scale Carbon Capture and Storage (CCS) project involves storing captured CO₂ emissions in deep saline aquifers, leveraging a geological solution suited to the region’s unique subsurface characteristics. One of the central innovations lies in its leak-detection capabilities, integrating RESMAN’s chemical tracer technology deployed for the first time in the UAE to monitor storage integrity and swiftly pinpoint any leaks.
A comprehensive monitoring framework with Measurement, Monitoring and Verification (MMV) capabilities provides the sensitivity, diagnostic capability, and economic viability required for large-scale CCS deployment. The system is built to last—operational for 30 years post-injection, covering every phase from active storage to long-term verification, delivering real-time insights to verify caprock integrity, quantify leaks, and trace their sources.
The monitoring solution
The monitoring solution centers on RESMAN’s High Integrity Detection System (HIDS), deployed across a network of shallow soil sampling boreholes surrounding the injection site. The system’s defining technical characteristic is its 0.1 parts per trillion (ppt) tracer detection threshold for CO₂ leakage events, enabled by capillary adsorption tubes (CAT) that undergo scheduled retrieval and laboratory analysis.
Tracer monitoring delivers multi-layered verification of storage integrity through three core functions. Continuous surface soil monitoring assesses caprock integrity and simultaneously verifying integrity of legacy wells for leaks to the atmosphere. During post-injection phases, the system maintains active surveillance of stored CO2 utilising the same principles. Advanced diagnostics provide precise leakage quantification and source identification, particularly crucial for multi-injector configurations, where determining CO₂ migration origins is essential.
Shallow boreholes positioned near injection wells monitor any effects the CO₂ injection might have on the geological structure, through surface gas and tracer detection across all operational phases. Radially distributed soil monitoring arrays track potential caprock breaches, with diagnostic algorithms distinguishing between multiple potential leakage sources. The 30-year monitoring protocol spans active injection through post-operational stewardship.
Implementation involves scheduled tracer injection into the CO₂ stream with periodic CAT sample retrieval for laboratory analysis. The system's integrated architecture correlates surface measurements with downhole data, providing leak quantification and source identification capabilities that surpass conventional pressure-based monitoring methods.
The system’s 0.1 ppt tracer detection sensitivity permits early identification of containment breaches at scales previously undetectable. Economic efficiency is achieved through optimized tracer volumes that reduce material requirements without compromising monitoring fidelity. The technology’s eighteen-year track record in continuous monitoring applications demonstrates long-term reliability under field conditions. These attributes collectively ensure compliance with stringent MMV requirements for industrial-scale CCS deployments.
Project implications
This initiative establishes several important technical precedents for regional CCS development. It demonstrates the viability of saline aquifers as secure storage reservoirs while providing a practical template for long-term MMV framework implementation. The cost-efficiency of the monitoring solution addresses a key barrier to CCS scalability in the Middle East. Furthermore, the project’s thirty-year monitoring horizon sets a benchmark for stewardship accountability in geological carbon storage.
This article is based on two recently published scientific papers:
SPE-222348-MS: Chemical Tracer for Soil CCS Monitoring Application: Monitoring CO2 Storage in Saline Aquifers Using Advanced Chemical Tracer and Detection Technology
SPE222367 -MS: Falaha CCS Project - Pioneering Low Carbon Solutions with CO2 Sequestration in Deep Carbonate Saline Aquifers
RESMAN delivers proven tracer-based MMV technology for CCS projects, with over 18 years of continuous carbon storage monitoring experience. For more information, please visit www.resmanenergy.com
Oil prices remain under pressure in the face of potential oversupply and uncertain demand, as OPEC+ rolls back output cuts
The eight OPEC + countries which previously announced additional voluntary adjustments (ie Saudi Arabia, Russia, Iraq, UAE, Kuwait, Kazakhstan, Algeria, and Oman) will implement a production adjustment of 548,000 bpd per day in August 2025 from the July 2025 required production level, in accordance with the decision agreed upon on 5 December 2024 to start a gradual and flexible return of the 2.2mn bpd voluntary adjustments starting from 1 April 2025. This is higher than the last three rollbacks of 411,000 bpd and means that OPEC+ is on track to fully unwind 2.2mn bpd of cuts nearly a year ahead of schedule.
“The gradual increases may be paused or reversed subject to evolving market conditions. This flexibility will allow the group to continue to support oil market stability,” said OPEC in a statement, noting “steady global economic outlook and current healthy market fundamentals, as reflected in the low oil inventories”. The eight countries will meet on 3 August 2025 to decide on September production levels.
“Investors remain cautious, especially as seasonal demand typically softens later in the year and US trade tensions intensify. President Trump’s upcoming tariffs, including a fresh threat targeting BRICS-aligned nations, added to the markets cautious tone,” commented global financial group MUFG, adding that the move marks a sharp shift from OPEC+’s past restraint.
“Opec+ keeps surprising the market,” said Jorge León, head of geopolitical analysis and senior vice president at energy consultancy Rystad. “This sends a clear message, for anyone still in doubt, that the group is firmly shifting towards a market share strategy.”
“It was pointless to maintain these voluntary cuts once the strategy became market share rather than price defence. But for the sake of appearances, and perhaps with the hope of managing market expectations, they have to go through the motions anyway, notionally unwinding the cuts at an incremental pace,” said Harry Tchilinguirian, group head of research at Onyx Capital Group in a LinkedIn post.
Suresh Ramanujan, vice president - Qatar, Kuwait, Iraq & Jordan at Emerson argues that technology and partnership are imperatives for achieving sustainable energy security
Achieving energy security is not necessarily in conflict with ensuring sustainability. Focusing on energy security at the cost of sustainable practices can only lead to short-term gains. Striking a balance is crucial especially in the context of a global transition to a low-carbon future. While renewable energy sources continue to grow in importance and influence, the transition cannot happen overnight. Liquefied natural gas (LNG) has emerged as a vital component of this shift — not as a competitor to renewables, but as a complementary, lower-emission fuel that supports reliability where intermittent sources fall short. With up to 50% lower carbon emissions than compared to other fossil fuels, LNG is a viable transition fuel that provides reliable energy for countries where renewables alone cannot meet current demand.
As countries prioritise both energy access and climate action, LNG is increasingly being integrated into long-term energy strategies. National development plans and capital projects around the world are scaling up LNG infrastructure to meet projected demand through 2035 and beyond. Shell's LNG Outlook 2024 predicts that global LNG demand will grow by approximately 50% by 2040, driven by emerging economies like India and Vietnam that are prioritising lower-emission energy sources to fuel their development while meeting climate commitments.
This raises a critical question: how can we scale LNG responsibly while lowering its environmental impact?
Qatar’s experience provides a good example of how to strike this balance. The nation is undertaking a massive North Field Expansion project that will boost its LNG production capacity from 77 million tonnes per annum (MTPA) to approximately 126 MTPA by 2027.
What makes this expansion noteworthy is its parallel commitment to sustainability. Qatar is investing substantially in carbon capture technology, with plans to sequester 9 million tons of CO₂ annually by 2030.
Technology as an enabler of sustainable energy
Advances in process optimisation, emissions reduction, and energy efficiency are transforming how LNG facilities operate, significantly improving their environmental performance.
The Qatargas Jetty Boil-Off Gas Recovery Facility exemplifies this approach. By implementing advanced automation technology provided by Emerson’s LNG Solutions Center in Qatar, the facility eliminates flaring at Ras Laffan, recovering 600,000 tons of LNG annually while reducing greenhouse gas emissions by 1.6 million tons per year.
Technology partnerships like this will be beneficial to supporting the energy transition in Qatar, and elsewhere in the world. Through advanced control systems, optimisation software from AspenTech, and precision instrumentation and valve technologies, Emerson enables LNG operators to run safer, more efficient, and more reliable operations. These solutions not only help reduce emissions and optimise energy use but also ensure process consistency across the entire lifecycle of LNG facilities—from design and commissioning to maintenance and digital transformation.
Innovations and expertise gained from such partnerships will enable businesses to achieve sustainability and operational excellence; it will also empower local industries with tools to remain competitive in a rapidly evolving global market.
Developing local expertise to address transition challenges
Technology alone, no matter how sophisticated, cannot drive sustainable transformation without the human expertise to implement and optimise it.
Qatar's National Vision 2030 recognises this reality, emphasising economic progression through innovation, sustainability, and human development. Emerson’s LNG Solutions Center is supporting this vision by providing programmes that will cultivate local expertise needed to facilitate the country’s transition to a carbon-neutral future. This provides immersive training environments where engineers and technicians can develop proficiency with cutting-edge technologies before implementing them in operational facilities. They create spaces for collaboration between operators, technology providers, and academic institutions. And they function as innovation hubs where solutions to industry challenges can be explored, tested, and refined.
Beyond production: the entire value chain
A comprehensive approach to ensuring a balance between energy security and sustainability must consider the entire LNG value chain – from production and processing to transportation and utilisation.
In transportation, for instance, the foremost considerations include solutions for safe transfer of liquefied gas as well as carrier operations. These are essential for maintaining safety and environmental integrity. Accurate containment monitoring and custody technologies can help ensure safe transfer when loading or unloading LNG, while specialised carrier systems support safety, environmental compliance, and reliability for LNG carriers.
At the consumption end, technologies that optimise combustion processes, minimise methane slip, and support fuel switching in power generation and industrial applications help maximise the environmental benefits of choosing natural gas over higher-carbon alternatives.
LNG in a net-zero future
LNG has the potential to remain valuable even in a highly decarbonised energy system. A number of factors support this view. First, the integration of carbon capture and storage technology can dramatically reduce the lifecycle emissions of natural gas. Second, existing LNG infrastructure can be repurposed for transportation and storage of hydrogen energy when this resource becomes more mainstream or as green and blue hydrogen production gains wider adoption. Finally, the reliability and disposability of gas-fired power generation make it an ideal complement to intermittent renewable energy sources like wind and solar.
Without a doubt, the path forward will require continued innovation in technology, policy frameworks and regulations, as well as market structures and business models. The balanced approach advocated here considers both the immediate necessity of reliable energy access and the imperative of addressing climate change.
-
GPT Industries - Iso-Smart
-
ADIPEC 2024 - Exclusive Interview with Joseph El Bitar, Hexagon
-
ADIPEC 2024 - Exclusive Interview with Alexander van Veldhoven, Bapco Energies
-
ADIPEC 2024 - Exclusive Interview with Friedrich Portner, Safeen Group
-
ADIPEC 2024 - Exclusive Interview with Kevin Brilz, Fishbones
-
ADIPEC 2024 - Exclusive Interview with Mohamed Malak, Fishbones
-
ADIPEC 2024 - Exclusive Interview with Dileep Divakaran, SLB
-
ADIPEC 2024 - Exclusive Interview with Eric Kjol, SLB
-
ADIPEC 2024 - Exclusive Interview with Dmitry Shubenok & Aleksandr Dolgikh, North Side
-
ADIPEC 2024 - Exclusive Interview with Adam Stephenson, AkzoNobel
-
ADIPEC 2024 - Exclusive Interview with Frazer Young, Oil States
-
ADIPEC 2024 - Exclusive Interview with Peter Foith, CS Combustion Solutions GmbH
-
Exclusive interview with Maurits van Tol
-
Rockwell Automation interview with Sebastien Grau
-
Rockwell Automation interview with Michael Sweet
-
ADIPEC 2023 - Exclusive interview with Wissam Chehabi, Fishbones
-
Rockwell Automation interview with Kalypso’s Rodrigo Alves & Knowledge Lens’ Ganesh Iyer
bp and Shell have signed agreements with Libya’s National Oil Corporation (NOC) to evaluate hydrocarbon redevelopment prospects in some of Libya’s major oilfields
Under the MoU signed by bp, the company will evaluate redevelopment opportunities in the mature giant Sarir and Messla oilfields in Libya’s Sirte basin, including the exploration potential of adjacent areas, and look at the wider unconventional oil and gas potential within the country.
The agreement provides a framework for bp to assess a range of technical data and to work with the NOC to evaluate opportunities and determine the feasibility of future development and exploration programmes.
William Lin, bp executive vice president gas & low carbon energy, said: “This agreement reflects our strong interest in deepening our partnership with NOC and supporting the future of Libya’s energy sector. We hope to apply bp’s experience from redeveloping and managing giant oil fields around the world to help optimise the performance of these world-class assets. We look forward to conducting thorough studies, working closely with NOC, to evaluate the resource potential of this promising region.”
The Sarir and Messla oilfields are among Libya’s largest, offering scope for a significant potential addition to bp’s Libya portfolio, according to a bp statement.
bp has confirmed its intention to resume operations in Libya and reopen its office in the capital, Tripoli, within the last quarter of 2025. bp resumed exploration in the onshore areas of Libya in 2023 after a 10-year joatis. along with a number of other international oil companies.
The MoU was signed at a ceremony in London, when Eng. Masoud Suleman, chairman of the NOC, welcomed bp’s return to operations in Libya and the expansion of the partnership between the two parties. He called for the cooperation between the NOC and bp to include training technical and leadership staff in Libya’s oil sector.
The NOC has also reached an agreement with Shell for the company to evaluate hydrocarbon prospects and conduct a comprehensive technical and economic feasibility study to develop the al-Atshan field and other fields fully owned by the NOC.
Libya is currently producing around 1.2mn bpd but is looking to bump this up to 2mn bpd by 2028. However, progress has been hampered by political unrest and factionalism in the aftermath of the civil war, and the existence of two rival governments. Libya is keen to attract international companies to redevelop its oil and gas sector, and there is significant international interest in its largely untapped hydrocarbon potential, as demonstrated by the number of bids submitted following the launch of its international bid round earlier this year, results of which are expected in around November. This offers 22 blocks for exploration and development (11 Offshore and 11 Onshore) including areas with undeveloped discoveries estimated to contain a minimum of 2.0 Bboe in hydrocarbon resources.
ADNOC Gas has entered into a US$400mn three-year LNG supply agreement with Germany’s SEFE Securing Energy for Europe, as it continues to expand its global business
The agreement is for the delivery of 0.7mn tonnes of LNG, which will be supplied from ADNOC Gas’ Das Island 6 mtpa liquefaction facility. It builds on the ongoing collaboration between the UAE and Germany, including the 2022 Energy Security and Industry Accelerator (ESIA) pact and the 2024 Joint Declaration with the state of Baden-Württemberg, both aimed at fostering energy security and sustainable fuel development.
Fatema Al Nuaimi, chief executive officer of ADNOC Gas, said: “This agreement marks a significant step in strengthening our long-standing partnership with SEFE and reinforces ADNOC Gas’ role as a reliable and responsible global energy provider, committed to supporting Germany’s energy security.”
Frédéric Barnaud, chief commercial officer of SEFE, said: “Over the past two decades, we’ve built a strong partnership with ADNOC, and we value our relationship with such a reputable and reliable supplier. This new medium-term LNG contract builds on the long-term supply agreement with ADNOC that we signed last year, thereby adding another flexible source of LNG to our portfolio – to the benefit of both Europe’s security of supply and our global market trading activities.”
As a lower-carbon energy source, LNG plays a critical role as a transition fuel. ADNOC has ambitions to significantly grow its LNG capacity and strengthen its position as a global LNG player, shipping LNG to a growing range of international markets in Asia, Europe and beyond.
Abu Dhabi-based petrochemicals company Borouge is collaborating with Honeywell to conduct a proof of concept for AI-powered autonomous operations, which is is set to deliver the petrochemical industry’s first AI-driven control room designed for full-scale, real-time operation
The initiative aims to deploy the proof-of-concept technologies to enhance Borouge’s operations across its Ruwais facilities in the UAE. Autonomous operations will enable Borouge to optimise production, reduce energy use, and enhance safety while reducing costs at what will be the single largest petrochemical site in the world. Both companies will leverage their expertise in process technology and autonomous control capabilities to identify new opportunities to deploy Agentic AI solutions and advanced machine learning algorithms.
The project is a key component of Borouge's companywide AIDT programme, which is projected to generate US$575mn in value this year. In 2024, Borouge’s portfolio of over 200 AIDT initiatives—spanning operations, health and safety, sales, sustainability, and product innovation—generated $573mn in value
Borouge has already installed the world’s largest Real-Time Optimisation (RTO) system across three large-scale ethane crackers and 20 furnaces. The initiative analyses over 2,500 parameters per minute, enabling instant data-driven decisions, significantly enhancing productivity, optimising energy consumption and reducing emissions. The unique system minimises ethane dumping and optimises resource use, in line with Borouge's commitment to sustainable growth and operational excellence.
Borouge has invested in its state-of-the-art Innovation Centre located in Abu Dhabi and is now using advanced AI-powered tools to accelerate innovation, enabling the company to bring new grades of advanced polymers to market quicker. In collaboration with ADNOC AI Lab, Borouge has completed its first “Polymer Optimisation” programme, achieving a 97% accuracy, enabling Borouge to reduce its development timeline from months to weeks.
Hazeem Sultan Al Suwaidi, chief executive officer of Borouge, said, “Borouge's AI, Digitalisation, and Technology (AIDT) transformation programme is setting new standards in operations, innovation and business performance. By collaborating with global AI leaders such as Honeywell, we are accelerating growth, driving efficiency, and enhancing shareholder value. This project further strengthens Borouge’s competitive edge as we continue to deliver on our ambitious AIDT roadmap.”
George Bou Mitri, president of Honeywell Industrial Automation, Middle East, Turkey, Africa, Central Asia, said, “By integrating AI and automation technologies into core operations, we are helping unlock new levels of efficiency, safety, and performance. This agreement shows how advanced technologies, applied with purpose, can reshape industrial operations at scale.”
Mohamed Zouari, general manager for the Middle East, Africa, and Turkey at global AI and data cloud company Snowflake, argues that the future of oil and gas hinges on integrating AI and data throughout the value chain
Energy, the driver of the global economy, is undergoing one of the largest shifts of our time, propelled by hundreds of trillions of dollars in global investment over the next 25 years. The Middle East, home to the world's lowest-cost producers and the largest reserves, is positioned at the heart of this transformation. According to OPEC, the region is forecast to provide nearly 60% of global oil exports by 2050.
Against this backdrop, Middle Eastern nations are embedding digital transformation in their national strategies. The UAE’s forward-thinking initiatives, like Masdar City, alongside Saudi Arabia’s giga projects under Vision 2030, illustrate the regional ambition to lead in innovation. With oil exports comprising about 30% of the UAE’s GDP alone, the stakes are high. Data and AI are emerging as vital tools in this evolution, enabling companies to modernise infrastructure, generate real-time insights, and align operational decisions with long-term business objectives. As energy companies navigate this landscape, data and AI are becoming critical enablers for growth, operational excellence, long-term resilience and informed strategy across the oil and gas value chain.
Navigating the digital age
While the opportunity is immense, oil and gas companies face several critical challenges on the path to transformation.
One major obstacle is the need to digitise ageing infrastructure. Decades-old grids and oil wells must now integrate with millions of IoT-enabled assets like wind turbines and solar panels, creating an influx of zettabytes of operational and information technology data that requires efficient ingestion, cleaning, and analysis to drive smarter, faster decision-making.
Extreme weather, geopolitical dynamics, and the variability of renewable energy sources are contributing to more volatile commodity markets. Stable long-term contracts signed with countries like China, Japan, and India offer some security, but sophisticated data analytics are crucial to managing financial exposure and mitigating risks. Enhanced by AI and ML, predictive models can now draw on both internal and external data sources to forecast price fluctuations and demand trends more accurately, helping companies navigate volatile markets with greater confidence.
Corporations now demand rigorous environmental, social, and governance (ESG) reporting, while consumers seek intuitive, tech-driven home energy systems. Energy service providers – from utilities to oil and gas firms – must be agile, transparent, and responsive or risk falling behind.
Compounding these challenges is the overwhelming volume of unstructured data, which now represents 90% of all data according to Snowflake’s Data Trends Report. Without a centralised, secure, and scalable data infrastructure, energy companies will struggle to extract actionable insights.
AI and data strategies in practice
Modern AI and data strategies are offering new pathways to navigate this complex environment. Organisations are moving beyond traditional data management toward platforms that can unify siloed information, enable seamless collaboration across ecosystems, and deliver near real-time insights at scale.
At the core of this transformation is the ability to bring together operational, financial, and customer data into a unified environment. By doing so, oil and gas companies gain a single source of truth that supports more informed decision-making across their entire value chain – from field operations to trading desks to customer-facing platforms.
AI is also fundamentally reshaping how companies approach forecasting, maintenance, and customer engagement. Machine learning models are increasingly used to detect anomalies in equipment performance, allowing for predictive maintenance that minimises costly downtime. In trading operations, AI-driven models help forecast commodity prices with greater accuracy, enabling companies to optimise their portfolios and manage risk proactively.
For personalised customer engagement, companies can leverage real-time customer data and generative AI capabilities to deliver tailored recommendations and intuitive energy management solutions, improving satisfaction and loyalty in a highly competitive market.
Organisations that focus on building robust data foundations are better positioned to drive tangible outcomes, from optimising asset utilisation to accelerating sustainability initiatives. Snowflake’s research shows that 92% of early adopters have already realised a return on their AI investments, and 98% plan to increase AI spending in 2025.
With AI’s contribution to regional economies forecast to grow between 20% and 34%, AI is becoming a blueprint for the next generation of energy operations. The ability to seamlessly integrate and analyse vast, diverse data sets in real time is becoming a decisive competitive advantage.
The next chapter
By embracing AI and modern data strategies, oil and gas companies can digitise operations, manage volatility, anticipate customer needs, and chart a course for long-term resilience and growth – a necessary shift as fragmented data infrastructures and talent shortages remain real hurdles.
In a world increasingly defined by energy transition, those who invest early in scalable data and AI capabilities will not just survive – they will lead. The region’s commitment to digital innovation positions it well to remain a global energy powerhouse well into the future.
Oil Review Middle East hosted a very well-attended webinar on 20 November on the future of offshore operations, in association with SAFEEN Group, part of AD Ports Group
The webinar explored the latest trends and challenges in the rapidly evolving world of offshore operations, focusing on groundbreaking innovations that are driving sustainable and efficient practices. In particular, it highlighted SAFEEN Green – a revolutionary unmanned surface vessel (USV), setting new benchmarks for sustainable and efficient maritime operations.
Erik Tonne, MD and head of Market Analysis at Clarksons, gave an overview of the offshore market, highlighting that current oil price levels are supportive for offshore developments, and global offshore capex is increasing strongly. The Middle East region will see significant capex increase over the coming years, with the need for rigs and vessels likely to remain high. Offshore wind is also seeing increased spending. Global rig activity is growing, while the subsea EPC backlog has never been higher, with regional EPC contracts seeing very high activity. Tonne forecast that demand for subsea vessels and other support vessels will continue to increase.
Tareq Abdulla Al Marzooqi, CEO SAFEEN Subsea, AD Ports Group, introduced SAFEEN Subsea, a joint venture with NMDC, which offers reliable and innovative survey, subsea and offshore solutions to support major offshore and EPC projects across the region. He highlighted the company’s commitment to sustainability, internationalisation and local content, and how it is a hub for innovations and new ideas, taking conceptual designs and converting them to commercial projects. A key project is SAFEEN Green, which offers an optimised inspection and survey solution.
Tareq Al Marzooqi and Ronald J Kraft, CTO, Sovereign Global Solutions ME and RC Dock Engineering BV. outlined the benefits and capabilities of SAFEEN Green as compared with commercial vessels, in terms of safety, efficiency, profitability and sustainability. It is 30-40% more efficient through the use of advanced technologies, provides a safer working environment given it is operated 24/7 remotely from a control centre, and offers swappable payload capacity. Vessels are containerised and can be transported easily to other regions. In terms of fuel consumption, the vessel is environment-friendly and highly competitive, reducing emissions by 90% compared with conventional vessels, with the ability to operate on 100% biofuel.
As for future plans, SAFEEN Green 2.0 is under development, which will be capable of carrying two inspection work-class ROVs simultaneously. A priority will be to collect data to create functional AI models for vessels and operations, with the first agent-controlled payload systems in prospect by around 2027.
To view the webinar, go to https://alaincharles.zoom.us/rec/share/mNHjZhAhQzn1sPzmFWZCgrq7_SckfLRcSb4w81I7aVlokO9sgHM_zVeOqgN3DgJS.bO4OIRqNeFP09SPu?startTime=1732095689000
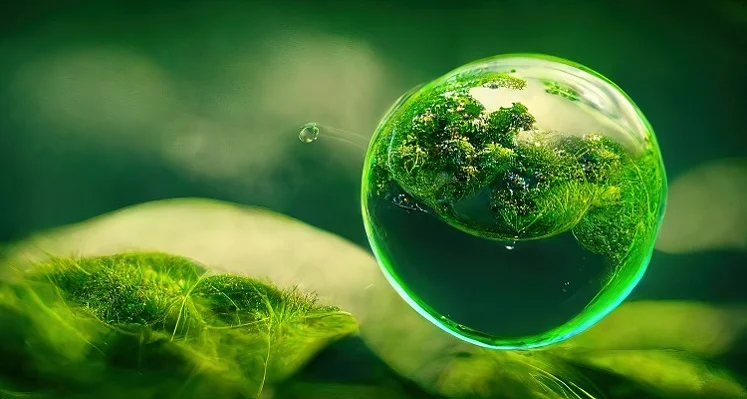
The UAE has launched its first initiative to inject CO₂ into deep saline aquifers for permanent geological sequestration.
Sven Kristian Hartvig, chief technology officer, RESMAN Energy Technology explains how the company’s advanced tracer technology is being used for CCS monitoring in Abu Dhabi’s saline aquifers
The UAE has launched its first initiative to inject CO₂ into deep saline aquifers for permanent geological sequestration. This inaugural industrial-scale Carbon Capture and Storage (CCS) project involves storing captured CO₂ emissions in deep saline aquifers, leveraging a geological solution suited to the region’s unique subsurface characteristics. One of the central innovations lies in its leak-detection capabilities, integrating RESMAN’s chemical tracer technology deployed for the first time in the UAE to monitor storage integrity and swiftly pinpoint any leaks.
A comprehensive monitoring framework with Measurement, Monitoring and Verification (MMV) capabilities provides the sensitivity, diagnostic capability, and economic viability required for large-scale CCS deployment. The system is built to last—operational for 30 years post-injection, covering every phase from active storage to long-term verification, delivering real-time insights to verify caprock integrity, quantify leaks, and trace their sources.
The monitoring solution
The monitoring solution centers on RESMAN’s High Integrity Detection System (HIDS), deployed across a network of shallow soil sampling boreholes surrounding the injection site. The system’s defining technical characteristic is its 0.1 parts per trillion (ppt) tracer detection threshold for CO₂ leakage events, enabled by capillary adsorption tubes (CAT) that undergo scheduled retrieval and laboratory analysis.
Tracer monitoring delivers multi-layered verification of storage integrity through three core functions. Continuous surface soil monitoring assesses caprock integrity and simultaneously verifying integrity of legacy wells for leaks to the atmosphere. During post-injection phases, the system maintains active surveillance of stored CO2 utilising the same principles. Advanced diagnostics provide precise leakage quantification and source identification, particularly crucial for multi-injector configurations, where determining CO₂ migration origins is essential.
Shallow boreholes positioned near injection wells monitor any effects the CO₂ injection might have on the geological structure, through surface gas and tracer detection across all operational phases. Radially distributed soil monitoring arrays track potential caprock breaches, with diagnostic algorithms distinguishing between multiple potential leakage sources. The 30-year monitoring protocol spans active injection through post-operational stewardship.
Implementation involves scheduled tracer injection into the CO₂ stream with periodic CAT sample retrieval for laboratory analysis. The system's integrated architecture correlates surface measurements with downhole data, providing leak quantification and source identification capabilities that surpass conventional pressure-based monitoring methods.
The system’s 0.1 ppt tracer detection sensitivity permits early identification of containment breaches at scales previously undetectable. Economic efficiency is achieved through optimized tracer volumes that reduce material requirements without compromising monitoring fidelity. The technology’s eighteen-year track record in continuous monitoring applications demonstrates long-term reliability under field conditions. These attributes collectively ensure compliance with stringent MMV requirements for industrial-scale CCS deployments.
Project implications
This initiative establishes several important technical precedents for regional CCS development. It demonstrates the viability of saline aquifers as secure storage reservoirs while providing a practical template for long-term MMV framework implementation. The cost-efficiency of the monitoring solution addresses a key barrier to CCS scalability in the Middle East. Furthermore, the project’s thirty-year monitoring horizon sets a benchmark for stewardship accountability in geological carbon storage.
This article is based on two recently published scientific papers:
SPE-222348-MS: Chemical Tracer for Soil CCS Monitoring Application: Monitoring CO2 Storage in Saline Aquifers Using Advanced Chemical Tracer and Detection Technology
SPE222367 -MS: Falaha CCS Project - Pioneering Low Carbon Solutions with CO2 Sequestration in Deep Carbonate Saline Aquifers
RESMAN delivers proven tracer-based MMV technology for CCS projects, with over 18 years of continuous carbon storage monitoring experience. For more information, please visit www.resmanenergy.com